Please contact [email protected] or call 1-888-707-5814 if you are unable to login.
Not a member? Sign up Sine Pump
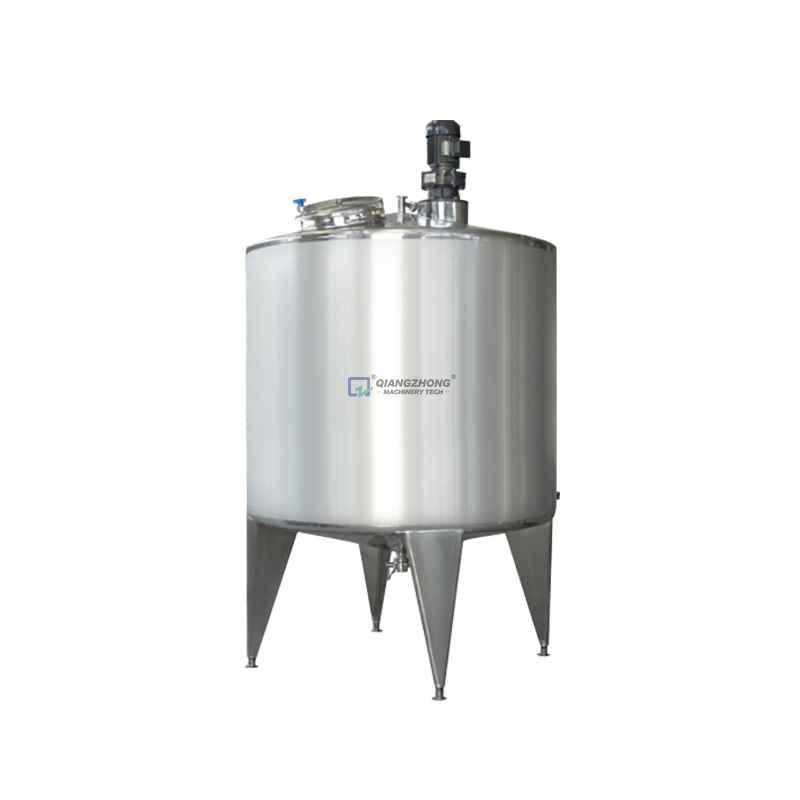
January 1, 2024 | By Scott Bryan and Julie Holmquist, Cortec
Understanding that viable strategies exist to protect essential cooling and heating systems from corrosion is a crucial step in ensuring proper asset protection
Several years ago, a manufacturing plant was forced to unexpectedly shut down one of its main production lines for several weeks. The cause: a rusty vacuum pump that pulled water through the cooling loop had corroded to the point of failure. Production on that line shut down for several weeks until a new pump could be delivered, costing the company not only the price of the new pump, but also the earnings that would normally have been generated if the manufacturing line had been in use. Perhaps the most troubling part of the problem was that the pump failure and line shutdown would have been completely avoidable had the manufacturer been using corrosion inhibitors in its cooling water. Unfortunately, the maintenance team was apparently unaware that this was even an option. With the discovery of the problem, the plant adopted a new water-treatment plan for the closed-loop system going forward, and also applied it to the company’s two other chiller systems [1].
The story above underscores the importance of engineers, facility managers and maintenance teams knowing their options when it comes to the proper upkeep of their process heating and cooling systems. Cooling and heating are integral parts of the chemical process industries (CPI), and without them, many processes simply cannot function. While one would hope that the natural ingenuity and problem-solving skills of mechanically-minded maintenance teams would know all the tricks of the trade to keep a chemical plant functioning optimally, this should not be taken for granted. In every industry, professionals must continue to learn and grow in their skills while staying abreast of technologies that can improve routine maintenance. One of these areas is corrosion protection, which can have a significant impact on the longevity of process heating and cooling equipment and whether or not unwelcome corrosion-related interruptions occur. Awareness of the proper tools for prevention can make a significant difference.
Heating and cooling play a variety of roles within the CPI. Mixing tanks where chemical reactions occur often need to be cooled down with a jacket of cooling water. In other cases, raw materials need to be heated up prior to mixing. For this purpose, many CPI plants have boilers that supply steam throughout the plant to appropriate points where heating is needed. Sometimes, chemicals that are manufactured must be stored at extremely cool temperatures and only heated up when they are ready to be applied. Fractionation towers at petroleum refineries are one specific example of a chemical process that relies on chillers, heat exchangers and reboilers to convert hydrocarbons into various products. The list goes on to encompass many other examples, including boilers and cooling systems used as part of heating, ventilation and air conditioning (HVAC) systems for comfort heating and cooling.
FIGURE 1. This compressor-based chiller does not operate in temperatures below 55°F. While the inside of the heat exchanger (cylinder at right) is made of copper and therefore is less likely to corrode, the outer shell is likely made of carbon steel and could therefore especially benefit from exposure to corrosion inhibitors during the off-season when coolant is sitting stagnant in the system
FIGURE 1. This compressor-based chiller does not operate in temperatures below 55°F. While the inside of the heat exchanger (cylinder at right) is made of copper and therefore is less likely to corrode, the outer shell is likely made of carbon steel and could therefore especially benefit from exposure to corrosion inhibitors during the off-season when coolant is sitting stagnant in the system
While many process heating and cooling systems remain in operation year-round, there are some seasonal changes that affect individual components or require seasonal layup of HVAC systems. One example is when plants switch between compressor chillers and air-cooled systems to regulate the temperature of their closed-loop coolants. Compressors located outside in regions with cold winters may not be able to operate when temperatures drop below 55°F for long periods of time (Figure 1). At this point, the plant may transfer over to an air-cooled system that takes advantage of cold or freezing outdoor temperatures to cool off the hot glycol passing through the chiller before it heads back into the building. This may mean switching back and forth seasonally between the pump that sends the coolant to the compressor-powered chiller versus the pump that sends it to the air-cooled chiller (Figure 2). As a result, one or more pumps or heat exchangers remain offline, either partially filled with stagnant coolant or empty altogether. This is a prime time for corrosion to occur if the cooling water is not properly treated. Seasonal facility heating or cooling changes also heighten corrosion risks for boilers or cooling towers that go offline for months at a time. It is often during these times of seasonal layup that corrosion strikes, because the normal operating chemical program is not in circulation.
FIGURE 2. This cooling loop uses multiple pumps. When the temperature drops below 55°F, the left pump kicks in to pump glycol to the aircooled chiller. When the temperature rises above 55°F, the right pump turns on to pump coolant to the compressor-powered chiller. Pump internals are often made of carbon steel or cast iron, making them good candidates for corrosion protection, especially during offline periods
FIGURE 2. This cooling loop uses multiple pumps. When the temperature drops below 55°F, the left pump kicks in to pump glycol to the aircooled chiller. When the temperature rises above 55°F, the right pump turns on to pump coolant to the compressor-powered chiller. Pump internals are often made of carbon steel or cast iron, making them good candidates for corrosion protection, especially during offline periods
A similar story can be true for backup equipment. Redundant pumps, meant to ensure that coolants or hot water keep flowing through the system if the primary pump fails, are more vulnerable to corrosion when temporarily offline — even if plants frequently alternate between pumps to reduce the risk. Unfortunately, a backup pump that is corroded and does not work properly can be as bad as not having a backup at all.
Another common piece of backup equipment is the steam-producing boiler kept on standby. This setup eliminates the need to refill or completely reheat the boiler water to keep the steam supply going if the primary boiler breaks down or has to be taken offline for routine servicing. While this backup plan minimizes interruptions to plant operations, typical methods of wet boiler layup require a great deal of maintenance work and may therefore go by the wayside. These methods also do not typically address corrosion concerns in the headspace above the boiler water where moisture may condense.
It is crucial that engineers understand that different types of metal have varying levels of corrosion risk. This is an important consideration for engineers designing the system, who must weigh the benefits of using a more expensive corrosion-resistant alloy, such as titanium or copper, against staying within budget by using cheaper but less corrosion-resistant metals, such as carbon steel and cast iron. Pumps and heat-exchanger shells are frequently made with carbon steel, while piping and internal heat-exchanger tubing are often made with copper or other more thermally conductive alloys. Once the system is designed and installed, maintenance personnel must be prepared to pay special attention to components made of metals susceptible to corrosion, although even yellow metals (brass alloys) can be at risk.
Vulnerabilities aside, what are the costs of corrosion in heating or cooling systems? The answers are many and varied. One common effect is that corrosion byproducts will migrate throughout the system, causing both fouling and the potential for even more corrosion sites to form. Furthermore, any metal loss from corrosion means a potentially shorter service life for the equipment. The buildup of corrosion products on heat-exchange equipment can significantly reduce a unit’s designed heat-transfer efficiency. If the corrosion is severe enough, it can cause equipment failure, opening up an entirely new set of problems. These new problems may include the cost of buying a replacement asset, the cost of labor needed for removal and installation and the cost of production lost while the equipment is out of operation. The bigger the operation, the higher the stakes, so prevention is almost always the more economical option.
Some common corrosion inhibitors for cooling loops include sodium nitrite, sodium molybdate and polymeric formulations [2, 3]. Among other things, one of the drawbacks of these treatments is that they do not provide corrosion protection in the vapor phase, neglecting protection for any area not in direct contact with the treated coolant (for example, pumps or systems that are offline and drained, or the headspace in pipes and systems that are partially filled). In the case of boiler layup, the use of quick lime or desiccant is common, with the main goal of absorbing as much moisture as possible. Boilers on wet layup or standby are often protected by keeping an elevated pH and higher sulfite residuals, an approach that requires frequent monitoring and does not address corrosion above the water level. Sometimes, nothing is done at all, accelerating the path to corrosion, downtime and shorter service life.
Another potentially more proactive approach is to use vapor-phase corrosion inhibitors, such as amine carboxylates, which work in both wet and dry systems. In addition to dissolving in the system fluid and protecting any metals in direct contact with it, these corrosion inhibitors also have the ability to vaporize and diffuse throughout small air pockets or large void spaces. This trait has obvious advantages for an empty backup pump, a cooling system that has been drained for the season or the headspace in a boiler on standby. These corrosion inhibitors, whether in vapor or liquid phase, form a protective molecular layer on the metal surface, interrupting the normal electrochemical reaction that takes place in the presence of metal, oxygen and an electrolyte. Protection is usually mixed, inhibiting a corrosion reaction at both the anode and cathode of a potential corrosion cell. Corrosion prevention with vapor-phase inhibitors takes many forms depending on the component and the stage of use. Some hypothetical examples follow.
FIGURE 3. Chemical reactions in this tank give off heat, requiring coolant to be piped into the reactor to cool the process down. Vapor-phase corrosion inhibitors are added to the coolant on a regular basis for corrosion protection of metals inside the closed loop
FIGURE 3. Chemical reactions in this tank give off heat, requiring coolant to be piped into the reactor to cool the process down. Vapor-phase corrosion inhibitors are added to the coolant on a regular basis for corrosion protection of metals inside the closed loop
Closed loops and pumps.Closed-loop cooling systems should be regularly treated with corrosion inhibitors as part of the normal chemical operating program (Figure 3). This reduces the risk for problems similar to those experienced by the manufacturer with the corroded vacuum pump mentioned at the opening of this article. Routine treatment with vapor-phase corrosion inhibitors also means that the system is prepared for times when, for example, the pump to the compressor chiller is turned off to allow the air-cooled chiller to take over. Protection will continue on metals in stagnant areas, as well as those that are not completely filled. With the right corrosion inhibitor selection, protection can also cover multiple alloys, including carbon steel, cast iron and copper, at once.
FIGURE 4. Amine-carboxylate based vapor-phase corrosion inhibitors protect below and above the fluid level, forming a protective molecular layer on metal surfaces
FIGURE 4. Amine-carboxylate based vapor-phase corrosion inhibitors protect below and above the fluid level, forming a protective molecular layer on metal surfaces
Boilers and steam systems.Redundant boilers kept on low fire can sometimes be protected with the same package of corrosion inhibitors used for closed-loop systems if the temperature is not extremely high. Compared to a traditional sulfite program, application of vapor-phase inhibitors is typically much safer and more convenient. The vapor-phase action takes care of protection above the water level, in addition to the protection that is going on below the water level (Figure 4). Frequent monitoring is not required, and the system can be turned back on at any time to continue necessary operations.
Boilers used for facility heating are often shut down and drained completely, constituting a dry boiler layup. The use of vapor-phase inhibitors at this stage is a major improvement on desiccant-only layups, which seek to minimize the source of the problem by absorbing moisture but not proactively fighting corrosion. If the desiccant is unable to absorb all the moisture present, corrosion may occur in spite of protective efforts. For extended shutdowns of 30 days or more, the desiccant should be monitored and replaced as necessary to maintain a moisture-free system. Workers must also be sure to remove the desiccant before putting the boiler into operation, or further complications will develop.
In contrast, protection with vapor-phase inhibitors is convenient, comprehensive and proactive. It can be as simple as placing a water-soluble pouch of vapor-phase inhibitors inside an empty boiler and slitting it open to allow the release of corrosion inhibiting vapors. As long as the boiler remains closed, these corrosion inhibitors actively protect all accessible metal surfaces within the boiler. One advantage is that the boiler does not have to be completely dry in order for the corrosion inhibitors to work. Another advantage is that bringing the boiler back online is as easy as filling the boiler back up since the corrosion inhibitor pouches simply dissolve in the boiler feedwater. For extremely large boilers, vapor-phase inhibitors are available as a waterborne fluid that can be fogged throughout the boiler and steam system, typically without requiring removal before startup.
Corrosion-inhibitor application for seasonal shutdown of cooling systems is usually slightly different. It often consists of adding the corrosion inhibitor to the system, circulating it and letting it stand for 24 h to allow the formation of a protective film on the cooling system walls. The loop can be left full for wet layup or drained for a dry layup. In either case, vapor-phase corrosion inhibitors remain to help protect all accessible internal areas of the system, provided the system openings are closed. Often, the alternative is either to do nothing or to hope that loading the system with corrosion inhibitors from the operational water-treatment program will provide protection even after the system has been drained — which is typically a fruitless effort unless amine-carboxylate-based corrosion inhibitors have been used.
The benefits of such corrosion avoidance and asset protection in the CPI are far-ranging. From reducing the high cost of downtime and sidestepping the complications of rust clogging to extending equipment service life and improving heat-exchanger efficiency, these benefits begin with simple awareness of the prevention measures that are available.
Edited by Mary Page Bailey
Special thanks to Cortec plant manager Adam Ramsey and Cortec service engineer Lisa Marston for providing technical support on this article.
All images courtesy of Cortec.
1. Cortec Corp., Preventing Corrosion in Chiller System Vacuum Pump, Case History #805, May 2023.
2. Daniels, D., Monitoring and Treatment of Closed-Loop Cooling Water Systems, POWER Magazine, March 2016.
3. Buecker, B. and others, Protecting Steam Systems from Corrosion, Chem. Eng., Feb. 2021, pp. 31–38.
Julie Holmquist (Email: [email protected] ) has been a content writer at Cortec Corp. since 2015. She specializes in writing about corrosion-inhibiting technology for a variety of industries, including manufacturing, oil and gas, power generation and water treatment.
Scott Bryan (Email: [email protected] ) is Cortec’s technical sales manager for water treatment products. He has almost 30 years of experience in the water treatment industry. Bryan has maintained his qualifications as a Certified Water Technologist (CWT) since 2005. For 15 years, Bryan worked as a distributor for Cortec water-treatment solutions before joining Cortec in 2019.
Join today to get all of CHEMICAL ENGINEERING
Chemical Engineering news and content delivered every week
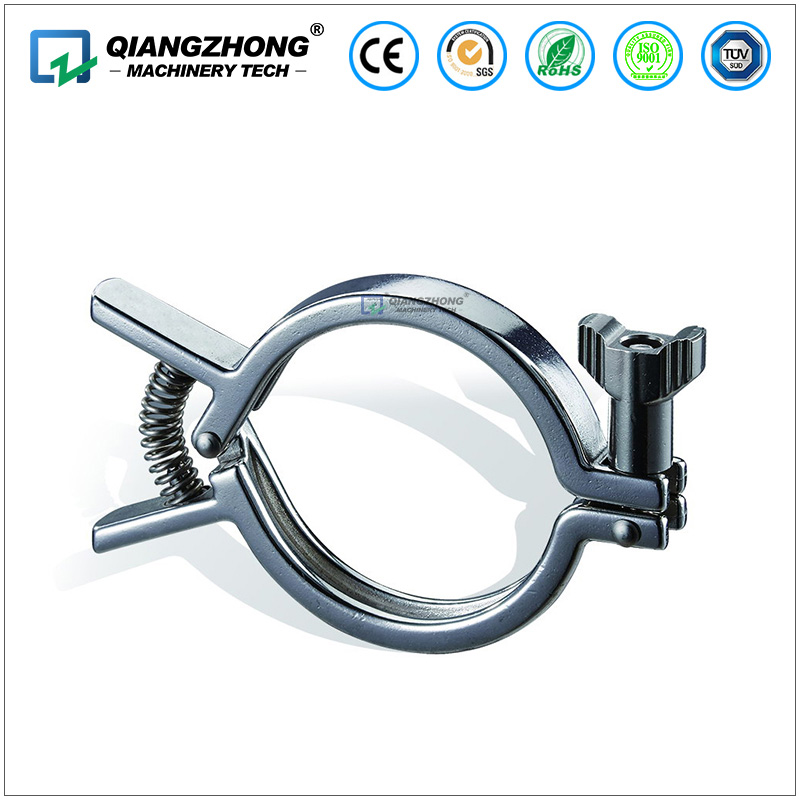
Mechanical Mixing Tank © Access Intelligence, LLC. All rights reserved. | Privacy Policy | Diversity, Equity, Inclusion & Belonging | Accessibility Statement