In a large industrial facility five miles from campus, a University of Georgia lab is at the forefront of researching the next generation of sustainable protective fabrics.
Originally funded by the U.S. Department of Defense during the pandemic to conduct research on N95 masks, the College of Family and Consumer Sciences’ Nonwoven Material Research Lab is one of just two university labs in the country capable of producing and testing such new materials for industry. Fine Gauge Wire Mesh
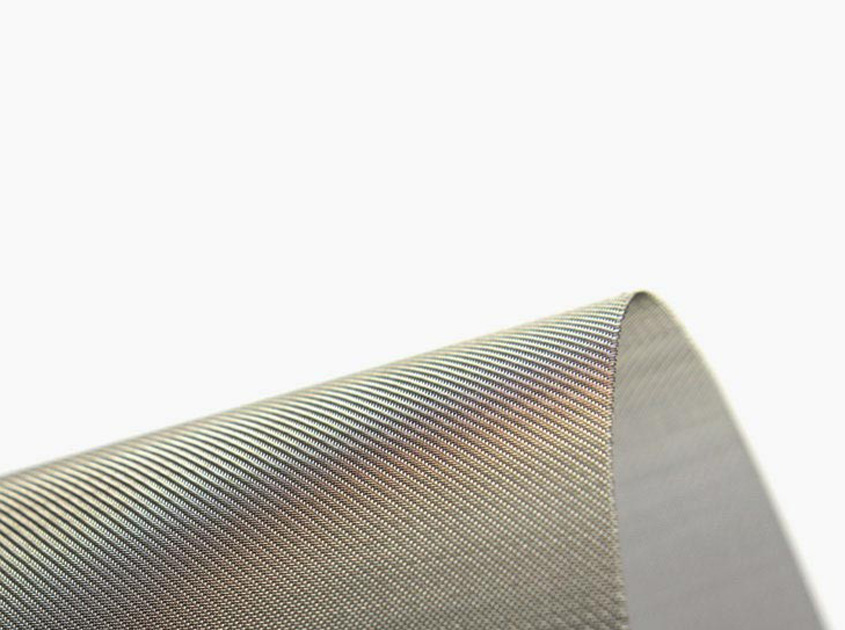
“I think the pandemic showed us the gap and the need for research and development,” said Gajanan Bhat, Georgia Athletic Association Professor of Fibers and Textiles and lab director. “Post-pandemic, although we don’t need N95 masks to the same extent, we are still talking about cleaner air in hospitals, nursing homes, workplaces, homes and air quality in general. There’s also pressure for industry to incorporate more sustainable materials.”
The centerpiece of the lab is the melt-blown equipment that converts a thermoplastic polymer into fine fibers – 500 times smaller than a a human hair – that create an optimal filter.
“Because of the thin fibers, you have high surface area and that’s what makes it a good filter,” said Bhat, head of the department of textiles, merchandising and interiors within FACS. “It not only removes particles effectively, but is also breathable.”
The goal of the lab is to attract both small-scale and larger industries to use its pilot lines to develop new, sustainable materials to use as filters that have the same or better particle filtration properties as traditional filters.
Bhat said some industries are already experimenting with bio-based, renewable resources like corn-based plastics and even natural fibers to create high-efficiency filters.
One such plastic created from these sources is called polylactic acid, or PLA, which is already commercially available and has similar properties to the more commonly-used polypropylene.
“One of the problems we see with petroleum-based filters is that all of this personal protection equipment, especially masks, are thrown away and stay in the environment forever, so we need to address the sustainability issue,” he said. “Renewable sources are bacteria-friendly, which means they are most likely biodegradable.”
In conjunction with the UGA College of Engineering, the lab recently partnered with a company developing a plastic using waste cooking oil in a project funded by Advanced Functional Fabrics of America, a national public-private consortium launched in 2016 to revolutionize the fiber and textiles industry.
Bhat said the filters created from these new plastics could potentially have a wide range of applications, from the biomedical and pharmaceutical industries to conducting research on the next generation of materials for car batteries.
“The way I see it, this lab is helping the industry not only in Georgia but all over the U.S. evaluate new materials,” Bhat said. “We have the idea and the vision and these companies can come here and run trials in our facility without sacrificing their production equipment. It brings the end product producer together with the supplier.”
UGA, industry partners team up in search of a more sustainable filter
Launched in June, the campaign raises awareness about the college's offerings
Study finds healthier foods can be made more appealing through a few simple steps
UGA Entrepreneurship pitch contest draws 52 student startups for their chance at $25,000 prize
Student designers in Laura McAndrews' class team with local physician to help solve complex issue
Fashion merchandising faculty, students honored at ITAA conference
Extension project focuses on education, outreach to address opioid crisis
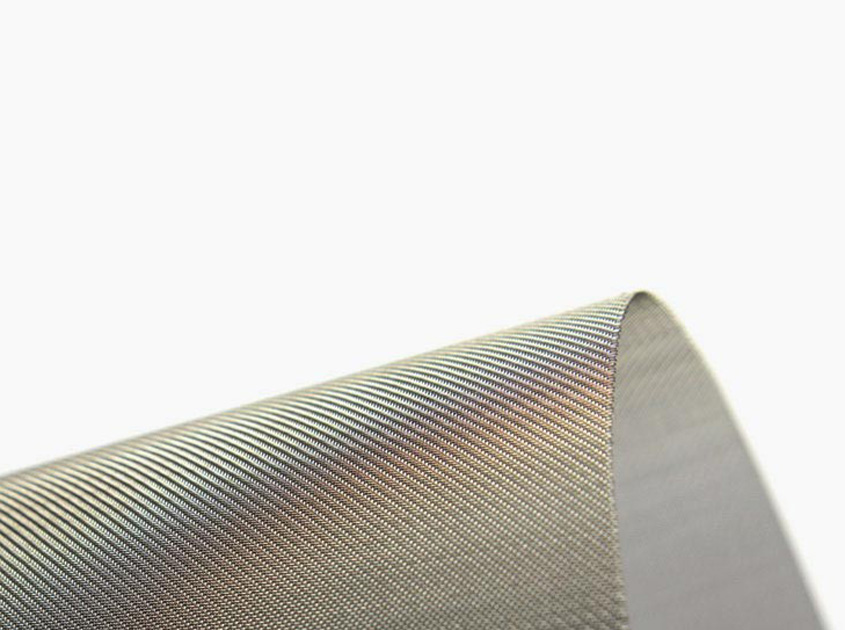
Filter Element 5 Micron FACS to sponsor four children as part of DFCS Angel Project