This article was updated April 14, 2023. It was originally published Nov. 15, 2002.
READ MORE: V-belt Selection it's a Veritable Cinch Cogged V Belt Teeth Belt
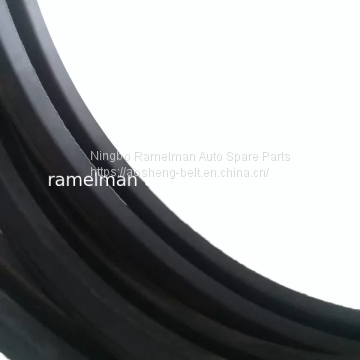
Belts have long been used to transfer rotary motion from one shaft to another. The belts were efficient, simple devices that found their way into many applications. But they had at least one deficiency; if an engineer wanted to synchronize one shaft’s motion to another’s, flat belts tended to slip at high speed and torque changes.
To solve this problem, one that was particularly prevalent in textile mills, engineers in the early 1940s developed the synchronized belt (also called the timing belt or, less commonly, a cambelt). The belts have a toothed profile that mates with corresponding grooves in the pulleys, thereby providing positive engagement such in chain or gear drives.
Trapezoidal teeth were used on the first synchronous belts and are now considered standard. The tooth design is derived from the spur gear, and they can provide precise positioning. Trapezoidal teeth are commonly used in machine tools, textile machinery, home appliances, business equipment, and as camshaft drives in engines.
READ MORE: Sustainable Engineering: Belts Beat Chains for Sustainable Operations
Over the years, mechanical engineers have devised an array of improved and specialized tooth profiles. The fully rounded profile called high torque drives (HTD), for example, more evenly transfers tooth loads more to the belt. The teeth also have more shear strength which lets the belt carry greater loads. Compared to the original trapezoidal teeth, HTD can deliver two to three times the power.
There’s also a modified curvilinear tooth design called STPD. It looks similar to the HTD design, but its pressure angle, tooth depth, and materials are chosen for increased loads and long operational life.
READ MORE: Keeping Belts in Synch
Belt durability and strength are crucial. That’s why many are made of economical and strong rubber. But for heavier industrial loads, manufacturers go with neoprene. And polyurethane belts work where rubber fails; they resist harsh chemicals, have higher tooth strength and can be machined into a variety of specialized profiles.
To keep the timing between shafts consistent, the synchronized belts must remain the same length throughout a long life of moving loads. To help with both consistency and durability, manufacturers added steel reinforcement fiber. Those were largely replaced by belts with glass-fiber reinforcements. For applications involving heavy loads, aramid fiber can boost the belt’s load capacity.
Engineers at Brecoflex combined polyurethane, specialty coatings, and steel reinforcements when they upgraded their AT8 MOV timing belt. The belts are FEA optimized and made of polyurethane with laminate coatings and galvanized steel tension members.
The upgrade improved stiffness and tensile strength by 75% and tooth shear went up 30%. These improvements let companies use thinner belts while maintaining the same load capabilities and safety margins. This makes the belt drive more compact and quieter.
READ MORE: Multi-Layer Metal Belts 101
Even if here’s no need to synch up a couple of shafts, synchronized belts have some features that could justify their use in many applications. Being thin and flexible, they are well suited for miniature drives and pulleys, as well as high speeds.
Some studies indicate they may be one of the most efficient forms of power transmission short of direct drive. In addition, they can also sustain high loads.
These characteristics have made timing belts cost effective in such nonsynchronous applications as drives for power saws, motorcycles, and vacuum-cleaner brushes.
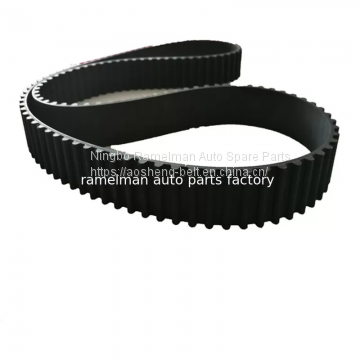
China Drive Belt The primary drawbacks of synchronous belts are their higher cost relative to other types. Technicians must also be skilled and careful installing the pullies, which must be accurately aligned.