All aggregate and mining operations with a wet processing plant will produce a waste stream. This waste stream consists of tailings – the process water and fine solids, clay and other deleterious material removed during the washing process. Traditionally, these tailings are sent to a settling pond or lagoon to separate the solids from the liquid in the waste stream.
However, settling ponds can be time-consuming and expensive to maintain, take up valuable land space and/or cover up mineable reserves. They are not the best method for tailings management, especially when mechanical dewatering options are available. Small Filter Press

Mechanical dewatering equipment improves tailings management by separating the solids from the liquid to produce a solids product that is suitable for mechanical handling. As an added bonus, the recovered water can be reused in the washing process, reducing freshwater requirements for sites where water is scarce or expensive.
Types of mechanical dewatering equipment for tailings include:
Decanter Centrifuges separate solids from liquid in a slurry by means of high centrifugal forces to induce sedimentation. The slurry enters the Decanter Centrifuge via a feed pipe into the inside of a rotating screw conveyor that is tapered at one end. The slurry is then released into a bowl surrounding the screw conveyor that is rotating at a higher speed than the conveyor.
High G-forces cause the solid particles in the slurry to be flung to the walls of the bowl, where the screw conveyor moves them toward the tapered discharge end. The tapered end of the screw allows the solids to dewater as they make their way toward the discharge. The water freely moves to the other end of the machine and discharges via ports.
Decanter Centrifuges produce a solid cake material that is suitable for mechanical handling as well as immediately reusable process water. They discharge a solid material somewhere between that of a Thickener and Filter Press. Decanter Centrifuges are fully automated and enclosed for cleaner operation.
Belt Presses feature rollers and belts to dewater material by passing the slurry through four main zones.
The first zone, the preconditioning zone, is where chemicals are added to draw the particles in the slurry together. The second zone, the gravity drainage zone, allows free water to drain from the slurry as it moves along an inclined belt. The third zone, the low-pressure squeezing zone, sandwiches the material between two porous belts, where liquid is squeezed out and the solids are retained between the belts. The fourth zone, the high-pressure squeezing zone, passes the belts under and over a series of rollers that decrease in diameter.
The result is a dewatered solids material that varies in consistency depending on the solids concentration of the feed.
Filter Presses provide the highest level of mechanical dewatering without the use of chemicals. They consist of a number of recessed plates covered with filter cloths. When the plates are clamped together hydraulically, the recesses form chambers. Slurry is pumped into the Filter Press and fills the chambers. The liquid in the slurry passes through the cloth and out filtrate pipes at the bottom of the plates to collect in a trough at the bottom of the Filter Press. The solids are captured on the filter cloth. When no more slurry can be pumped into the Filter Press, the pump is stopped, and the plates open to release the solid cakes.
These solid cakes are drip-free, stackable and can be easily handled by loading and/or hauling equipment. Depending on the material, it can potentially be sold as a backfill or pond lining. The recovered water is then immediately available for use in the wash plant upstream.
Which is the Best for Tailings Management?
When it comes to tailings management, the best equipment for one site may be different than the best equipment for another site. Decanter Centrifuges, Belt Presses and Filter Presses are all suitable choices for pond reduction/elimination, so the best one depends on the tailings management goals of the site.
The main thing to consider is the type of material being dewatered. Decanter Centrifuges work best with material that has a larger particle size distribution and is more easily dewatered. They are also ideal for material with low clay content, and they are less sensitive to changing feeds.
Belt Presses can be used to dewater a variety of different slurries in a wide range of applications, but they don’t perform well with varying feed conditions.
Filter Presses are ideal for dewatering tailings from mineral and aggregate wash plants, mineral concentrates and most underflow slurries coming from a Thickener or clarifier. However, the feed percent solids and particle size distribution do have an effect on the overall dewatering efficiency of a Filter Press.
Some additional things to consider include maintenance and operation, as well as the costs associated with those tasks.
In terms of operational costs, Decanter Centrifuges and Filter Presses are fully automated, whereas Belt Presses require an operator.
Filter Presses do not require the addition of chemicals to aid in dewatering, while Belt Presses do. Decanter Centrifuges may benefit from the use of chemicals, but that depends on the material being dewatered.
Decanter Centrifuges have higher power requirements than Belt Presses and Filter Presses, so electrical costs will be higher with these units. Decanter Centrifuges also tend to produce more noise than a Belt Press or Filter Press.
In terms of capital cost, Belt Presses are generally less of an upfront investment when compared with Centrifuges and Filter Presses. Additionally, Filter Presses require ancillary equipment, such as a surge (or buffer) tank. Depending on the upstream equipment employed, Belt Presses and Centrifuges may not. Belt Presses and Centrifuges can operate on a continuous basis, so no surge tank is required to feed the machine. Slurry is continuously fed into these machines, and they continuously discharge solids. Filter Presses, on the other hand operate in a batch process. A pump feeds the slurry into the machine and stops when the plates are opening to discharge the solid cakes. The feed material needs somewhere to accumulate while the plates are opening, hence the need for a surge tank.
Maintenance costs are higher with Belt Presses because maintenance intervals are more frequent than Centrifuges and Filter Presses. Belt Presses require frequent belt washing, and the rollers and bearings are known for requiring frequent replacement, which means more downtime to perform maintenance.
In terms of footprint, Belt Presses and Centrifuges take up less space than Filter Presses.
When determining which solution is right for handling your tailings, make sure you consider the type of material the equipment will be processing as well as the initial investment and long-term operational and maintenance costs.
With market-leading print and digital platforms for the Recycling, Quarrying, and Bulk Material Handling Industries we provide a comprehensive, and virtually unique route to market. Our bi-monthly magazine is available in print or electronic mediums delivering the latest news on new product launches, and industry projects directly to individually addressed on-site locations throughout the UK & Northern Ireland. Such is the demand we enjoy a regular pass-on readership of 2.5 providing a total of in excess of 15,000 regular readers of the magazine.
We work closely with companies to provide on-site editorials focusing on their clients feedback. All wrapped up with on-site recorded interviews, professional photography, delivering dynamic stories and images that enhance the stories. We also attend open days & events and promote these by writing engaging editorial pieces published in our magazine, website & e-newsletter. Let HUB-4 distribute magazines at your open day and we'll promote your event for you in the news and events section of our website prior to the event.
Our bi-monthly magazine is sent directly to 6,000+ quarries, recycling sites and bulk handling plants, with a pass-on rate of 2.5 giving an estimated readership of 15,000 throughout the UK.
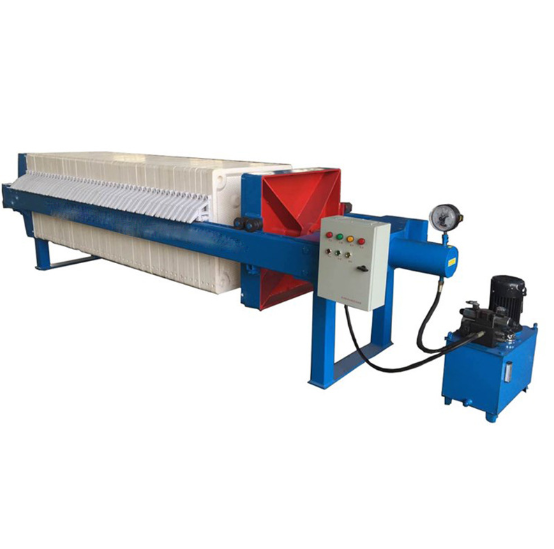
Fractionation Filter Press © 2024 HUB Digital Media Ltd |Registered at Companies House, Company No: 5670516.