A s a technical consultant, I have seen various new technologies implemented in both new and old applications. In the semiconductor industry, WBG devices such as SiC and GaN transistors have been gaining attention due to their small size, fast speed, and better thermal performance. The introduction of these new semiconductors into the consumer market came after a series of military and other commercial applications of the technology in everything from electric vehicles to radar systems.
GaN devices have enabled a much better form factor for product design than their silicon counterparts. As they become cheaper and more available, it is expected that we will see them widely adopted in power-switching modules worldwide. Mc4 Cable

Technically speaking, GaN semiconductors are high-electron-mobility transistors (HEMTs), meaning they do not have the doped region in a PN junction like MOSFETs. This enables faster electron flow, hence higher switching speed. Because HEMTs do not have the PN structure, they also do not have a body diode. This can have a great impact in applications such as motor drives, where we can now switch on the HEMT for freewheeling rather than relying on the body diode.
From the EMC perspective, this feature can be useful as, traditionally, EMI issues associated with the reverse recovery charge of a body diode during deadtime can be a problem [1]. To fix the issues, engineers often place a Schottky diode in parallel with the MOSFET as Schottky diodes switch faster and do not have a reverse recovery charge effect [1]. Now that the switching speed of a GaN is faster than a Schottky diode, it does not have a reverse recovery charge effect either. The HEMT has a “quasi diode” mode in the deadtime region, and we need to control the deadtime well.
But new technology often presents a double-edged sword. The most significant advantage of a GaN device (superfast switching, say 100V/ns) also brings a challenge for controlling EMI. As we all know, the faster the switching action (i.e., defined by the rise time), the harder it is to contain EMI, especially above the frequency of 1/πt, where t is the rise/fall time of a switching event. This can be seen in Figure 1.
Figure 1: Near-field probe measurement of two switching devices, the device under test is a forward converter, with a duty ratio close to 50%.
Facing an EMC test failure, many engineers have chosen to swap the WBG device with a silicon MOSFET to pass EMC tests, considering time-to-market is often critical for companies to profit. But this defeats the spirit of making a higher-efficiency product. Facing greater EMI challenges, many engineers choose to “flight” rather than “fight” under time and cost pressure.
In other cases, engineers have chosen to use silicon MOSFETs based on trade-off calculations in the design. For instance, if using a WBG device results in requiring an additional filter to pass EMC, it is not a good idea as the filter would add cost and weight. But, given a good product design with EMC consideration in the design stage, it is believed that a WBG device should be the device of choice, supporting efforts to achieve the best possible product form factor and resulting in higher performance and lower cost. This can already be seen in the laptop/mobile phone charger market, where GaN chargers have started dominating the market.
The main EMI challenges in WBG-based power converters can be summarized as shown in Figure 2. These challenges can be categorized into different frequency ranges:
Figure 2: Common EMC test failures seen in applications with wide band gap devices
In addition to the EMI challenges mentioned earlier, there are other EMC-related concerns in such applications. These include low-frequency harmonics and immunity to surge and electric fast transients (EFTs). To improve harmonics and power quality performance, incorporating a power factor correction (PFC) circuit in the front end can be beneficial and has become a general practice in mains-powered products. A front-end filter can enhance immunity to surge and electric fast transients. This will be explored in more detail later.
Before delving into the design techniques for WBG device applications, it is essential to touch on the subject of benchtop tests and troubleshooting, which become more expensive and critical due to the unique characteristics of WBG devices:
Moreover, the cost and lead time associated with taking the unit to an anechoic chamber for EMC tests adds further challenges to the development process. For companies with limited budgets, the high cost associated with developing new technology should not become a stumbling block. Therefore, we present here some effective and low-cost benchtop test methods that can often achieve reasonably accurate results. These methods are summarized in Table 1.
The test set-up for Option 1 is illustrated in Figure 3, where the device under test is a GaN transistor-controlled, mains-powered power supply. Conducted emission testing using a LISN is relatively straightforward, and the method of using an RF current monitoring probe to predict far-field emissions is detailed in [5].
Figure 3: Proposed benchtop EMC tests, (a) measuring conducted emissions, and (b) measuring common mode current on cables to predict far-field emissions
For the Option 2 test setup, it’s worth noting that one can accurately measure the rise time without the need for an expensive probe. Instead, a near-field magnetic field probe (even a simple homemade one like the 2 cm field loop in Figure 4) can be employed [6]. The significant advantage of this non-contact method is that it avoids direct electrical connections to the circuit under test, thereby eliminating common measurement errors.
Figure 4: Using a near-field magnetic field loop to determine the switching characteristics
Common-mode noise currents have the ability to flow between an isolated output ground (often referred to as 0V_gnd or secondary ground) and the power supply input ground (commonly known as HV- or primary ground). These currents can attain considerable amplitudes, leading to Ldi/dt voltage drops between the grounds. Additionally, when both input and outputs are wire-connected to the source and the load, these wires function as efficient dipole antennas.
A near-field probe can also serve to estimate the emissions level, although not with pinpoint accuracy; however, we can rely on some useful rules of thumb. For instance, as illustrated in Figure 5, using a square-shaped, near-field probe (with a measuring side conductor length of 1 cm in this case) to measure the potential difference between the primary and secondary “ground,” any voltage exceeding 50 mV (I normally use 50 mV/cm rule) would be cause for concern in passing CE/FCC emission tests.
Figure 5: A 1 cm magnetic field loop can be used to predict far-field emissions
In this section, we will delve into the converter design, front-end filter, and shielding techniques, taking a GaN transistor-based charger as an example.
For chargers below 100 watts, the most popular topology is an active-clamped flyback converter. On the other hand, for chargers above 100W, the design of choice often involves an LLC with a PFC converter. Despite the topology specifics, we can generalize this type of isolated power supply as depicted in Figure 6.
Figure 6: A simplified isolated power supply circuit
In converter design, WBG devices find their primary application in the switching circuit on the primary side, including the PFC circuit (if present). However, on the secondary side, due to the lower voltage requirements, engineers tend to favor the use of MOSFETs for synchronous switching. As the power level increases, achieving this is often accomplished by either putting MOSFETs in parallel or employing interleave methods. To ensure the best EMC performance given design constraints, engineers should focus on three areas:
Figure 7: (a) a magnetic flux band around a transformer (b) High-voltage ceramic capacitors enjoy lower ESR & ESL at high frequencies, making them perfect for WBG applications. However, it’s worth noting that at low frequencies, the ESR is high, courtesy of TD
As of now, these obstacles prevent the practical replacement of electrolytic capacitors with high-capacitance ceramic capacitors.
If not designed properly, significant ringing can be observed on the primary side switching with a GaN/SiC device. The ringing frequency depends on the stray inductance in the design (often the transformer leakage inductance) and the parasitic capacitance of the switching device. To reduce this ringing, considerable effort should be focused on the following approaches:
Since the primary switching event contributes significantly to high differential mode noise in the low-frequency range, minimizing the DC link impedance is crucial. This can often be achieved by optimizing the layout between the DC link and the switch. Additionally, utilizing spread spectrum techniques can help reduce low-frequency conducted emissions. From a control perspective, incorporating zero voltage switching (ZVS) as a feature in the control chip can lead to reduced switching loss and EMI.
It is worth noting that a control feature such as ZVS can sometimes introduce noise in light load conditions. It is the design engineer’s job to check the EMI performance in all operation modes (light and heavy loads).
Considering the EMC challenges posed by WBG devices, the front-end filter plays a crucial role in ensuring the product passes EMC tests. While the MOV and in-rush current limiter designs follow standard processes, special attention must be given to the RF filter design.
Employing a two-stage filter is critical. The low-frequency conducted emission failures seen in the evaluation board (in Figure 2) occur due to the sole use of a one-stage filter. The capacitors used in the front-end filter should be film-type. For a more effective solution, a typical two-stage filter should incorporate two types of common mode chokes as key magnetic components:
The sectional wound common mode choke, with its numerous turns and flat wire winding, unavoidably possesses high turn-to-turn capacitance, rendering it unsuitable for high-frequency suppression. However, it boasts a high leakage inductance, allowing for add-on differential mode filtering.
On the other hand, the bifilar wound common mode choke, designed for high‑frequency filtering, cannot have too many turns. Its bifilar winding configuration wound on a toroidal core offers minimum leakage inductance (close to zero), making it ideal for high common mode noise suppression. Figure 8 illustrates both types of common mode chokes used in a charger.
Figure 8: Two types of common-mode choke used in a front-end filter; photo taken from a 140 W Apple charger
By strategically combining these two-stage filters with different choke designs, a comprehensive and effective front-end filter can be achieved, ensuring successful EMC performance for WBG-based devices.
In a GaN charger, a thin aluminum or copper sheet is often employed to further enhance EMC performance. While the metal’s thickness means it may not be as effective for low-frequency magnetic fields, the shield serves its purpose due to the following reasons:
This article aims to educate design engineers who are tasked with creating a product using wide-band-gap devices like GaN or SiC transistors. We’ve introduced the EMC challenges associated with WBG devices and propose cost-effective benchtop tests and troubleshooting methods. Additionally, we’ve presented useful design techniques that design engineers can follow to ensure their product’s compliance when conducting EMC tests for the first time.
Dr. Min Zhang is the founder and principal EMC consultant of Mach One Design Ltd, a UK-based engineering firm that specializes in EMC consulting, troubleshooting, and training. His in-depth knowledge in power electronics, digital electronics, electric machines, and product design has benefitted companies worldwide.
Your email address will not be published.
Save my name, email, and website in this browser for the next time I comment.
In Compliance is a leading source of news, information, education, and inspiration for electrical and electronics engineering professionals.
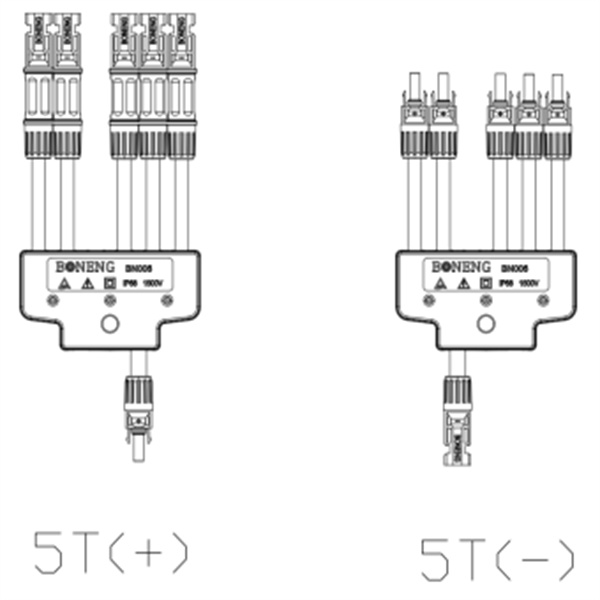
Weatherproof Electrical Junction Box Aerospace Automotive Communications Consumer Electronics Education Energy & Power Industrial Information Technology Medical Military & Defense