Integrating the Internet of Things (IoT) with lockout/tagout procedures is necessary because they are outdated despite being essential.
by BOSS Editorial | Published: September 21, 2023 | Updated: September 21, 2023 10:06 am China Lockout and Valve Lockout
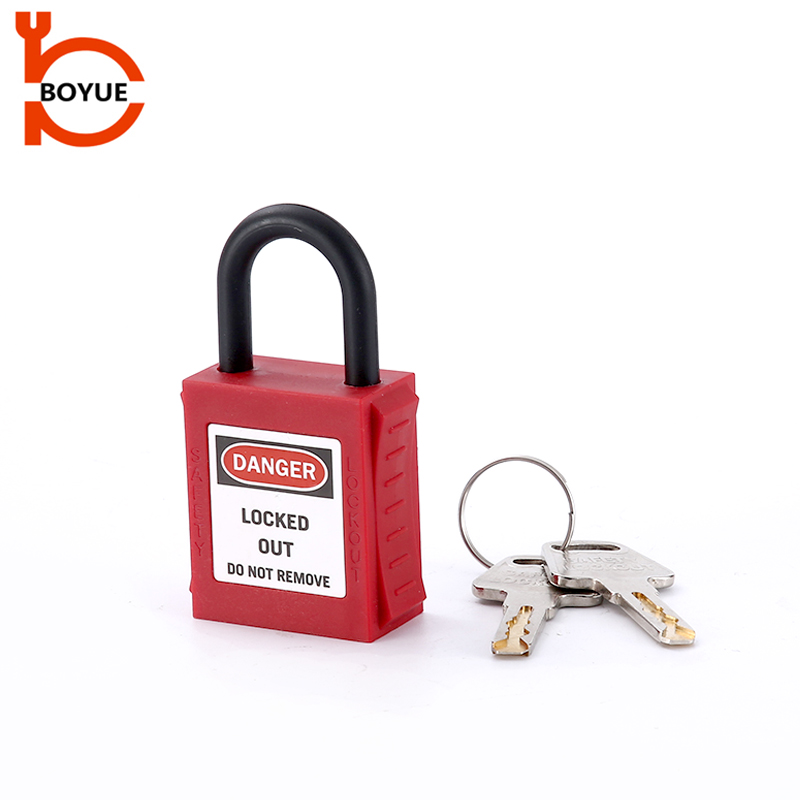
As more industries leverage modern technology for day-to-day operations, they must also recognize the importance of improving conventional lockout/tagout procedures. Technical innovations are far overdue for them. Luckily, the Internet of Things could be a game-changer.
Integrating the Internet of Things (IoT) with lockout/tagout procedures is necessary because they are outdated despite being essential. Even though they are an integral part of life for many professionals, they have long avoided most technological innovations.
The issue with traditional lockout/tagout procedures is their inconvenience and poor reliability. Since they often require manual interaction and do not connect to a network, they are not as safe as they should be. For example, a worker could physically bypass procedures or move forward without adequately locking the machinery.
Improper operation is often the cause of serious injuries, whether someone forgets to remove compressed air from a machine or apply their lockout hasp. In fact, one-third of all workplace accidents stem from a faulty lockout/tagout procedure. It is one of the most common safety violations because it relies on outdated technology and can get overly complex.
Hazard minimization should be the top priority when dealing with heavy machinery maintenance because it can result in bodily harm. In the United States, there were 2.6 million non-fatal workplace injuries in 2021 alone. Conventional procedures are only growing more obsolete with time, so safety managers and facility supervisors must take matters into their own hands.
Whether through indirect or direct integration, IoT vastly improve conventional lockout/tagout procedures. The futuristic capabilities of this technology offer many impressive benefits. Businesses can digitize their processes instead of simply using physical devices like tags, cables, hasps and padlocks.
IoT-integrated lockout/tagout devices are beyond simple safety tools — they allow workers to effectively communicate remotely with their supervisors. For example, they could report a potential fault to the safety manager and prevent the employee from moving forward with maintenance. The data-driven updates enhance their interactions because they ensure everyone is on the same page.
Supervisors can automate their record-keeping process since IoT technology can automatically record information for them. Instead of using a physical checklist to examine their tools and machinery, they can let the digital device do most of the work for them. It could immediately gather and categorize instances like equipment failure or procedure non-compliance.
Once they build a large enough collection of historical data, they can gain unique insights into their equipment functionality. For example, they could use it to collect operational or safety statistics. They could use their newfound knowledge to create data-driven reports, improving their machine efficiency.
Businesses stand to save a substantial amount of money when they integrate IoT with lockout/tagout procedures. Most of their preventable losses come from downtime, noncompliance and payouts — all things an interconnected digital device could fix. In fact, they paid nearly $1 billion every week in worker’s compensation because of accidents. If they use modern, interconnected devices, they could minimize their spending to an impressive degree.
Proper lockout/tagout procedures rely on communication and notification — the Occupational Safety and Health Administration (OSHA) even states all employees must be in the right positions or away from the work zone completely. While keeping track of everyone with conventional tools can be challenging, IoT technology provides a straightforward solution.
Once a business integrates IoT sensors into its operations, it can monitor employees’ positions and statuses in real time. Tracking everyone working on the machinery and in the surrounding area lets them immediately intervene when something goes wrong. Essentially, it acts as a digital emergency stop switch if they enter hazardous zones or do not comply with procedures properly.
Most IoT devices can automatically message supervisors or managers to inform them of any relevant news. For example, it could alert them of machine tampering or unauthorized attempts to bypass lockout/tagout procedures. Since it can report on mistakes and potential equipment failures, managers can find solutions incredibly quickly.
Whether a worker accidentally wanders into a hazardous area or forgets a step during the maintenance process, safety managers will know about it immediately. If that is not promising enough, this technology can also report on its own malfunctions. For instance, it can alert the user of an unstable network connection. It gives them a glimpse into the future and helps them prepare for almost any scenario.
Since IoT technology has a constant network connection, safety managers can use it to record employees as they proceed through the lockout/tagout procedure. Even if they have the utmost faith in their workers’ abilities to perform maintenance properly, it is still a fantastic feature. They can use it for future training or to identify areas of improvement, potentially increasing productivity and safety.
Performing maintenance on heavy machinery always comes with the potential for serious injury, so facilities should work to minimize their employee’s exposure. Luckily, IoT integration gives them a unique insight into repair timelines. Through data collection, the connected devices can detect and flag typical signs of equipment failure far in advance. Best of all, workers will enjoy getting extended breaks from complex step-by-step safety procedures.
Workers tend to move slowly during a lockout/tagout procedure because their safety is on the line — or they have to deal with nonsensical instructions. Either way, productivity is not something they typically worry about. However, IoT technology may change the way they approach machine maintenance.
Already, researchers have found ways to secure performance improvements. For instance, one team experienced tremendous progress after developing an IoT tool for 230V AC electrical devices. It performed lockout/tagout procedures almost 100% faster on average than the conventional equipment. The tests were wildly practical and exist as an impressive proof of concept.
IoT technology is a modern, innovative tool employers can use to protect their employees and equipment. Since conventional devices are long overdue for an upgrade, safety managers and facility supervisors should seriously consider integrating it. Its versatile and unique benefits make it one of the best solutions available.
Emily Newton is the Editor-in-Chief of Revolutionized Magazine, an online publication that explores innovations in science and technology.
Your email address will not be published. Required fields are marked *
By blending local presence with global reach to secure and simplify supply chains, today’s Fastenal creates value for their customers in 25 countries.
On the cusp of their 20th year in operation, KCH has evolved from a small trucking company into a leader in supply chain management and optimization.
In 2022, U.S. ecommerce sales topped $1 trillion for the first time, and this year 1 in 5 retail purchases in the world is made online. It’s been an ecommerce explosion.
Integrating the Internet of Things (IoT) with lockout/tagout procedures is necessary because they are outdated despite being essential.
Companies have to carefully evaluate and sometimes reshape their global ecommerce policies. Here are five things brands must consider when expanding their reach.
This guide discusses what affects a fleet’s performance and how supply chain professionals can enhance efficiency.
People are increasingly interested in making purchases online. Find out how to make sure your e-commerce business stays resilient during this surge and beyond.
Over the recent period of time, most of the businesses have made pledges to abide by regulations of maintaining the sustainability of supply chains.
With an acquisition ceiling of over $3 billion, FEMA’s disaster supply chain is the third largest supply chain in the federal government behind the Department of Defense and the Department of Veterans Affairs.
The foresight and diligent work that went into building the continent's first B2B ecommerce platform has WIN SOURCE positioned as the largest distributor of electronic components in Asia.
Sustainable supply chains need the data to help them adapt and green technologies that allow them to lower their emissions footprints and meet their ESG goals.
It’s hardly surprising that AI is also starting to influence the world of facilities management. Here are a few of the areas in which we can expect to see AI have a tangible impact.
Digital Ink 5050 Avenida Encinas Carlsbad California 92008
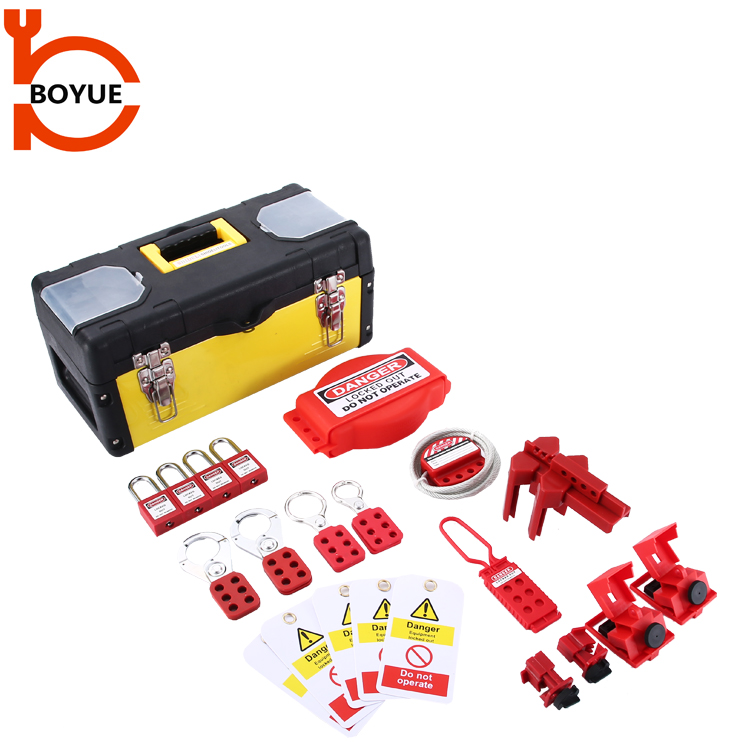
Lockout Box Copyright 2022 © BOSS Magazine ( a Digital Ink brand ) All rights reserved. Privacy Policy | Cookie Policy | Terms of Use