Home » Intelligent Filling Machine Lubrication for the Beverage Industry
One of the most critical applications determining overall OEE in beverage manufacture is the filling machine itself. This article explores a new approach and considers the potential of automated lubrication systems and food-grade lubricants in beverage-filling machines. Water Treatment System
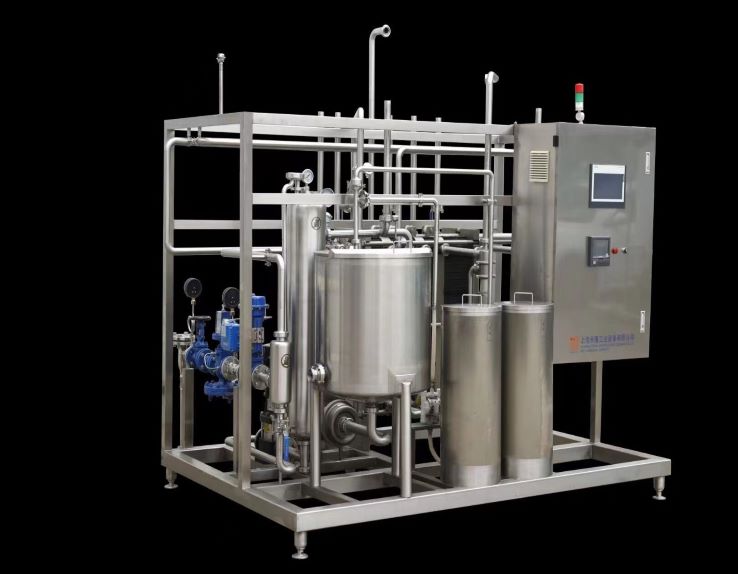
By Carlos Valderrama, Global Offer Manager for the Food and Beverage Industry within SKF Lubrication Management. He supports several customers in ensuring smooth, safe operations.
The growing demand for drinks at convenient locations: work, school, gym, transport, leisure – is being driven by the global trend towards urbanization, fuelled in turn by inexorable population growth. Inevitably, snowballing consumption increases the pressure on manufacturers, and also on the machines upon which they rely.
Small wonder that the beverage industry is becoming increasingly competitive. It is common for manufacturers to demand 24-hour production, leaving little time for maintenance and requiring upkeep to be performed while equipment is still in operation. Machine failures have a dramatic impact on availability – the goal of overall equipment effectiveness (OEE) at 80% or higher often clashes with a reality of around 60%.
One of the most critical applications determining overall OEE in beverage manufacture is the filling machine itself. Faced with filling a glass bottle, can, pouch, tube, PET and more with anything from water or tea to smoothies and yogurt, the market expects filling equipment that is accurate, versatile, hygienic, and reliable, even when operating continuously, at high speeds, and without planned maintenance breaks.
This article explores a new approach and considers the potential of automated lubrication systems and food-grade lubricants in beverage-filling machines. These characteristics of beverage production demand efficient lubrication of moving parts. SKF customers in the sector often list the following aspects of lubrications critical to the performance of filling machines.
Centralized, automatic lubrication systems (ALS) have the potential to increase machine availability while reducing reliance on scarce talent. These systems provide the appropriate quantity of lubrication at the correct intervals, minimizing friction and wear and optimizing bearing and machinery service life. Designed to lubricate individual machines or entire plants, ALS provides proper, precise lubricant replenishment to all required points, enabling a range of benefits in the process.
An intelligent machine, made from non-corrosive materials, therefore has the potential to eliminate the common problems listed above. By delivering the correct lubricant, in the right quantity, at the right time to the correct lubrication point, automation removes human error, hugely simplifies lubrication management, reduces lubricant consumption, and thereby enhances the overall efficiency of the bottling process.
Before we describe the different types of automated systems for filling machines, let’s examine the main factors that determine the correct choice of solution:
Factory environment: In most circumstances, stainless-steel components are essential to avoid corrosion. However, not all automated lubrication systems use corrosion-free materials.
Single-line automatic lubrication systems
A pump delivers lubricant to an (adjustable) metering device that services the lubrication points, delivering a precise amount of grease or oil. Single-line lubrication systems can be used to service one machine, different zones on one machine, or several separate machines. Monitoring is done by sensors that monitor system pressures and send signals to the control unit at preadjusted critical values. The control unit enables lubrication to be triggered automatically at predetermined intervals. Single-line lubrication systems can serve up to 900 lubrication points in machines over distances of up to 100 meters. Smaller systems are fed by compact pump units and lubricant reservoirs, bigger systems are fed by barrel pumps. Installation is easier than with a progressive grease lubrication system, but the initial investment in a single-line grease lubrication system may be higher.
Progressive automatic lubrication systems
This is the most common lubrication system in the food and beverage industry. It can be used on small to medium-sized machines with dispersed lubrication points that require varying quantities of grease or oil. Progressive lubrication systems consist of a pump connected to a primary metering device, outlets from which are connected via pipes or high-pressure hoses to the lubrication points of the filling machine. The pump supplies lubricant to the meter, which splits the lubricant into predefined amounts, which in turn are pumped to the lubrication points or – alternatively – to the inlet of a secondary metering device, thereby enabling more points to be lubricated. Progressive lubrication systems can dispense a precise, metered amount of lubricant to up to 150 lubrication points over distances of approximately 15 meters.
Although there is an initial cost to installing an ALS, the return on investment can come faster than might be assumed. Firstly, labor costs are significantly reduced. But there are also considerable savings from reduced downtime and extended component life. There is no need to stop the machine for lubrication, only to keep the system filled and maintained, so efficiency is enhanced. Lubrication that takes place while the bearings are rotating also improves the distribution of lubricant. A small amount of grease remains flowing, keeping out contamination even when the machine is operating in a harsh environment.
Smart sensors and digital measuring devices also make it possible to constantly monitor the entire lubrication process. Monitoring and control are essential to the efficient operation of lubrication systems. Installed in conjunction with intelligent monitoring devices, automatic lubrication systems can facilitate economical and optimal lubrication. The resulting data can give operators advanced warning of lubrication or machine failure, enabling preventive action to be taken. The potential of automatic lubrication systems for filling machines can be measured in economic terms:
There are a number of benefits of automated lubrication systems:
Regulation is increasingly affecting global food and beverage production, with stricter rules food processors to change their processes or modify their machines. In some countries, stainless steel is already obligatory for critical machine parts. Components for use in damp areas must be corrosion-free and amenable to high-pressure cleaning. Health concerns are also rising with regards to the use of inappropriate lubricants in the manufacture of food and beverage products. Lubricants themselves must therefore be certified safe for incidental contact with items to be consumed by humans, and compliant with the dietary specifications of the world’s major religions. Upgrading to automated lubrication can bring the additional benefit of compliance with existing or anticipated regulations. Components must be coated in stainless steel or housed in a stainless steel cabinet, ensuring that migration of contaminants takes place, if at all, in completely harmless amounts.
SKF and Lincoln lubrication products, systems and services are available through a global network of distributors, supported by a unified sales organization around the world to offer turnkey solutions and extensive aftermarket support, including food-grade lubricants tailored to the beverage sector. We are committed to your success through optimizing your lubrication management.
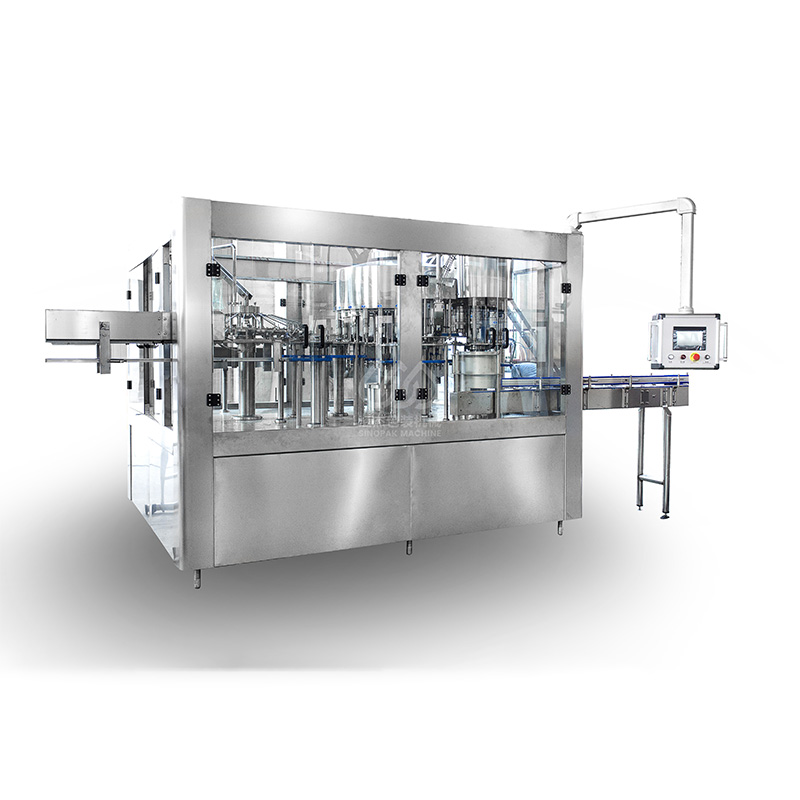
Water Filling Machine Industry News for Business Leaders